Vehicle Safety
A Deep Dive into Safety Belt Webbing: Materials and Strength
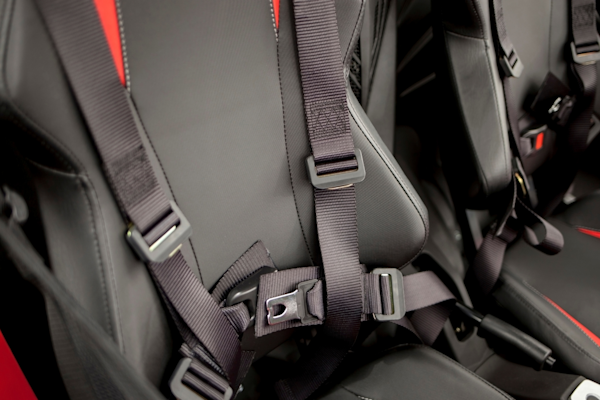
A Deep Dive into Safety Belt Webbing: Materials and Strength
Safety belts, commonly known as seat belts, are critical components in automotive safety systems. They are designed to protect passengers in the event of a collision by restraining their movement and preventing serious injuries. The webbing of a safety belt plays a pivotal role in its effectiveness. In this article, we will explore the materials used in safety belt webbing and delve into the strength and durability aspects that ensure passenger safety.
Materials Used in Safety Belt Webbing
Safety belt webbing is crafted from high-strength materials designed to endure significant forces without tearing or stretching excessively. The most commonly used materials include:
1. Polyester
Polyester is the most widely used material for safety belt webbing. It offers an excellent balance of strength, durability, and elasticity. Polyester fibers are resistant to UV rays, moisture, and mildew, making them ideal for automotive applications. This material can withstand high loads and provides the necessary flexibility to absorb impact forces effectively.
2. Nylon
Nylon is another popular material used in safety belt webbing, especially in older models. It is known for its superior strength and elasticity, which allows it to absorb and distribute impact forces efficiently. However, nylon is more prone to degradation due to UV exposure compared to polyester. As a result, its use has diminished over time in favor of more durable alternatives.
3. Aramid Fiber
Aramid fibers, such as Kevlar, are occasionally used in high-performance safety belts. These fibers boast exceptional tensile strength and heat resistance, making them suitable for demanding applications. However, due to their high cost, aramid fibers are typically reserved for specialized safety equipment rather than standard automotive seat belts.
The Strength of Safety Belt Webbing
The strength of safety belt webbing is a crucial factor that determines its ability to protect passengers during a collision. Several aspects contribute to the overall strength of the webbing:
Tensile Strength
Tensile strength refers to the maximum amount of force that a material can withstand without breaking. Safety belt webbing must possess high tensile strength to endure the forces generated during a crash. Polyester webbing, for instance, typically has a tensile strength of around 5,000 to 6,000 pounds, ensuring it can hold up under extreme stress.
Weave Pattern
The weave pattern of the webbing also influences its strength. A tightly woven pattern enhances the webbing's ability to handle stress and distribute forces evenly across its surface. Common weave patterns include plain weave, twill weave, and satin weave, each offering different levels of strength and flexibility.
Durability
Durability is another critical aspect of safety belt webbing. The material must resist wear and tear, especially given the frequent use and potential exposure to harsh conditions such as sunlight, moisture, and temperature fluctuations. Polyester webbing excels in durability, making it the preferred choice for most modern safety belts.
Ensuring Safety and Compliance
Automotive manufacturers must adhere to stringent safety standards and regulations when producing safety belt webbing. Organizations such as the National Highway Traffic Safety Administration (NHTSA) and the International Organization for Standardization (ISO) set specific requirements for the performance and quality of seat belts. These regulations ensure that safety belts can provide adequate protection in various scenarios.
Safety belt webbing is an essential component of automotive safety systems, designed to protect passengers by restraining their movement during a collision. The choice of materials, including polyester, nylon, and aramid fibers, greatly impacts the strength and durability of the webbing. By understanding the materials and strength factors involved, manufacturers can produce safety belts that offer reliable protection, ultimately saving lives on the road.
A Deep Dive into Safety Belt Webbing: Materials and Strength
Safety belts, commonly known as seat belts, are critical components in automotive safety systems. They are designed to protect passengers in the event of a collision by restraining their movement and preventing serious injuries. The webbing of a safety belt plays a pivotal role in its effectiveness. In this article, we will explore the materials used in safety belt webbing and delve into the strength and durability aspects that ensure passenger safety.
Materials Used in Safety Belt Webbing
Safety belt webbing is crafted from high-strength materials designed to endure significant forces without tearing or stretching excessively. The most commonly used materials include:
1. Polyester
Polyester is the most widely used material for safety belt webbing. It offers an excellent balance of strength, durability, and elasticity. Polyester fibers are resistant to UV rays, moisture, and mildew, making them ideal for automotive applications. This material can withstand high loads and provides the necessary flexibility to absorb impact forces effectively.
2. Nylon
Nylon is another popular material used in safety belt webbing, especially in older models. It is known for its superior strength and elasticity, which allows it to absorb and distribute impact forces efficiently. However, nylon is more prone to degradation due to UV exposure compared to polyester. As a result, its use has diminished over time in favor of more durable alternatives.
3. Aramid Fiber
Aramid fibers, such as Kevlar, are occasionally used in high-performance safety belts. These fibers boast exceptional tensile strength and heat resistance, making them suitable for demanding applications. However, due to their high cost, aramid fibers are typically reserved for specialized safety equipment rather than standard automotive seat belts.
The Strength of Safety Belt Webbing
The strength of safety belt webbing is a crucial factor that determines its ability to protect passengers during a collision. Several aspects contribute to the overall strength of the webbing:
Tensile Strength
Tensile strength refers to the maximum amount of force that a material can withstand without breaking. Safety belt webbing must possess high tensile strength to endure the forces generated during a crash. Polyester webbing, for instance, typically has a tensile strength of around 5,000 to 6,000 pounds, ensuring it can hold up under extreme stress.
Weave Pattern
The weave pattern of the webbing also influences its strength. A tightly woven pattern enhances the webbing's ability to handle stress and distribute forces evenly across its surface. Common weave patterns include plain weave, twill weave, and satin weave, each offering different levels of strength and flexibility.
Durability
Durability is another critical aspect of safety belt webbing. The material must resist wear and tear, especially given the frequent use and potential exposure to harsh conditions such as sunlight, moisture, and temperature fluctuations. Polyester webbing excels in durability, making it the preferred choice for most modern safety belts.
Ensuring Safety and Compliance
Automotive manufacturers must adhere to stringent safety standards and regulations when producing safety belt webbing. Organizations such as the National Highway Traffic Safety Administration (NHTSA) and the International Organization for Standardization (ISO) set specific requirements for the performance and quality of seat belts. These regulations ensure that safety belts can provide adequate protection in various scenarios.
Safety belt webbing is an essential component of automotive safety systems, designed to protect passengers by restraining their movement during a collision. The choice of materials, including polyester, nylon, and aramid fibers, greatly impacts the strength and durability of the webbing. By understanding the materials and strength factors involved, manufacturers can produce safety belts that offer reliable protection, ultimately saving lives on the road.